In this section
Supporting businesses
PAS 7050 supports businesses in bringing safe products to market; PAS 7100 supports businesses with corrective actions and recalls; and PRISM can help with the development of a risk assessment to provide support with a corrective action, recall or general decision-making (risk management). A 'corrective action' is something that is done to reduce the risk of harm from a product that has been found to be unsafe - for example, a product recall or a repair.
This is imperative for any business, especially those that want to have a safe product and satisfied customers. Improving product safety and quality can be key in preventing product returns, injuries and - even worse - fatalities. This, in turn, is not only the right thing to do, but can save businesses money and support them in complying with legal obligations.
Product safety management plan
A 'product safety management plan' (PSMP) is a plan that identifies the key processes, documents and contacts in relation to the production and supply chain for any product, which will help ensure that it is safe. It will vary from organisation to organisation and may have a different naming convention; however, any PSMP should consider the following:
- management commitment. Demonstration and commitment from management to product safety, allocating the necessary resources
- product safety management culture and training. An evident product safety culture; training should be provided where appropriate
- monitoring the regulatory environment and market conditions. Processes in place to monitor changes in product safety legislation, standardisation and what constitutes compliance
- clarity of supply chain responsibilities. Agreements with supply chain partners on product safety-related responsibilities
- supplier risk assessment and management. Processes in place for risk assessment of suppliers and how to manage identified risks
- product risk assessment and management. Processes in place for completing product risk assessments, identifying product compliance, testing and reviewing labelling
- manufacturing. Assessment and risk of variation throughout manufacturing, including the identification of critical control points and production processes to ensure that they remain in control and products are safe
- product traceability. Arrangements in place to allow for product identification if an issue arises
- monitoring product safety performance in the marketplace. A review of how products perform in the market. This could include how consumers are interacting with the product (consumer reviews / complaints), as well as identification of any potential product safety issues and how these may be addressed
- product safety incident plan. A plan on how to deal with an incident, should one occur (PSIPs are covered in detail in PAS 7100)
- safety throughout the product life cycle. Products should remain safe throughout their expected product life cycle and use
- review process. A review of the PSMP should take place to ensure that the plan and all related documents and processes are fit for purpose, particularly after any product safety incident
Most organisations will have their own processes for managing product risk, which may be similar to the above. Some may be more detailed than others, but the key is to have a plan in place that is useful and understood by all relevant members of staff, and that the processes and documents that support it are integrated and well-established throughout the business. This may be new for some businesses and more common for others, but it should be a plan that is part of the culture of the business and not something that is there to 'tick a box'.
Product safety incident plan
A 'product safety incident plan' (PSIP) identifies the key processes, documents and contacts in relation to a product safety incident. (As mentioned above, the PSIP is the focus of PAS 7100, which should be read alongside PAS 7050.) It forms part of the PSMP and covers similar topics. These plans will vary in each organisation and may have a different naming convention; however, any PSIP should consider the following:
- management commitment. This is similar to the PSMP noted above
- product and customer traceability plan. As noted above for the PSMP (in the 'product traceability' bullet point), arrangements should be in place to allow for product identification in the event of a product safety issue. Records of customer contact details should also be maintained (where practical and proportionate). Product traceability provides the means of distinguishing products that are, or may be, unsafe from those that can be confidently assumed to be safe. It also identifies where such products have been supplied to or are being stored, so that they can be isolated, reworked, withdrawn from the market or recalled from consumers. Additionally, good traceability allows quality and conformity assessment documents to be easily associated with products that are placed on the market, which provides an opportunity for regulators, such as Trading Standards officers, to verify that a product batch is safe
- product safety monitoring plan. Processes in place to review how products perform in the marketplace, how consumers are interacting with the product (consumer reviews / complaints), and identification of any potential product safety issues and how these may be addressed
- legal notification plan. This should include details on who to contact and what information to provide. There is a legal duty to notify the relevant regulator
- risk assessment plan. Processes in place for completing product risk assessments
- corrective action decision plan. Clearly setting out how decisions on corrective actions should be made and who will make them
- communication plan. Establishing mechanisms to ensure a comprehensive communication plan is in place, including content, responsibilities and communication channels
- training plan. Similar to the PSMP training, this should be provided where relevant
- testing plan. The PSIP should be tested with a simulated recall and other corrective action exercises
- review plan. Similar to the PSMP, the PSIP should be reviewed to ensure that the plan and all related documents and processes are fit for purpose, particularly after any product safety incident
Regulators
Part II of PAS 7050 provides recommendations to regulators that are supporting businesses with the development and implementation of a PSMP. In addition to responding proportionately where businesses fail to meet their legal obligations, regulators have an important role in supporting product safety and protecting consumers.
Although it is aimed at regulators, this part of the PAS document is also useful for businesses, helping them to understand the role that regulators play. Businesses can consult with the relevant regulator in the development of their PSMP or PSIP. This can be done through a Primary Authority, where applicable; see 'Primary Authority' for more information on this system.
Checklists
PAS 7050's annexes A to E include checklists for the various economic operators. These checklists are intended to support businesses and regulators when developing, implementing or reviewing a PSMP. These are provided as guidance only and can be adapted to fit the business they are referring to. They can be used as an aide memoire or perhaps an agenda list when discussing PSMPs.
The annexes appear in PAS 7050, but annexes A to E are also attached below in Word for businesses to use as a template for their own PSMPs:
- annex A is for all businesses. The subsequent annexes should be used in addition to this one
- annex B is for manufacturers
- annex C is for online marketplaces
- annex D is for repairers and refurbishers
- annex E is for distributors and importers of second-hand products
Annex F is an informative annex and includes information on technical and other documentation that supports compliance. This demonstrates the importance of technical documentation, also known as a technical file, which can vary depending on the product and the legal framework it sits under. This is a vital read for those who want to understand more about technical documentation, and the roles that both conformity assessment and the documentation itself play in ensuring that only safe products are brought to the market.
Annex G is another informative annex, this time on due diligence; in particular, it focuses on the 'due diligence defence', which is a key concept in product safety regulation. In the UK, many areas of the criminal law on consumer protection include the concept of 'strict liability', where it is irrelevant whether the accused did or did not intend to break the law in order for criminal liability to be established; someone who accidentally broke the law may be just as liable as someone who knew what they were doing. The due diligence defence is normally included in the legislation containing offences of strict liability.
To use this defence, a person establishes that they took "all reasonable steps and exercised all due diligence" to avoid an offence being committed. The defence includes broad principles, including the principle that sitting back and doing nothing is normally insufficient. Annex G also explores further broad principles that have been established regarding the due diligence defence. It is essential that those who want to understand more about due diligence read this annex.
Creating your own plans
In summary, any economic operator who works with products, whether it be a manufacturer, importer or distributor, should consider a PSMP and a PSIP.
Read the PAS 7050 and PAS 7100 documents, and if you then need help or support with the development of your plans, contact your local Trading Standards service.
PRISM
The PRISM methodology is intended for non-food consumer products. A guide and toolkit are available on the GOV.UK website, which also has examples of completed risk assessments for six products:
- non-compliant cords and drawstrings identified in clothing intended for children (less than serious risk)
- non-compliant portable juice blender (less than serious risk and covers multiple hazards)
- non-compliant toy with a detachable part (less than serious risk)
- non-compliant car seat
- non-compliant room / space heater
- non-compliant remote control for lighting chain
The PRISM toolkit (see link above) is an Excel spreadsheet that you can use to calculate your risk probabilities and the steps you are going to take. This should be supported by a rationale document (as shown with the six examples above) to explain your justification for each probability.
OPSS also provides some open-source data (again, see link above) to support risk assessment, which can be used to help with probability estimation and the development of injury scenarios.
How do PAS 7050 and PRISM relate?
PAS 7050 focuses on pre-market processes and PRISM is a post-market risk assessment methodology. PRISM is similar to the EU method, which is governed by Regulation (EU) 2024/3173 with regard to rules on access to and operation of the Safety Gate Rapid Alert System, information to be entered in that System, notification requirements and the criteria for assessment of the level of risk. Until 26 March 2025, Decision (EU) 2019/417 laying down guidelines for the management of the European Union Rapid Information System 'RAPEX' also applied in the EU; it is still a useful additional tool. Please note that, post-Brexit, neither of these are GB law.
See below for a visual explanation of how PAS 7050 and PRISM relate.
Pre- vs post-risk assessment
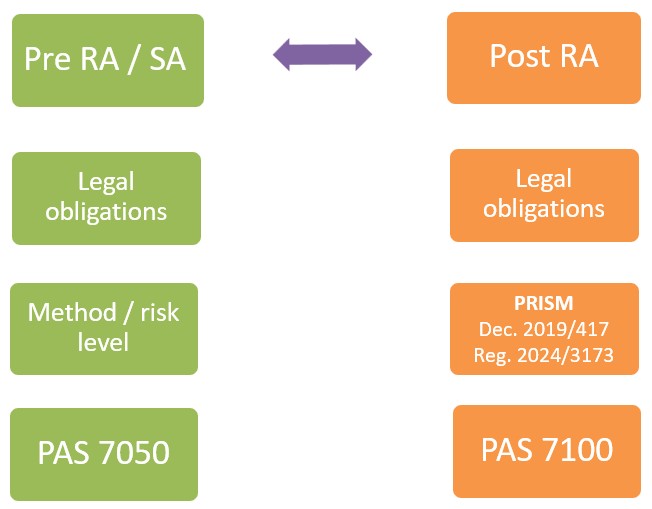
Pre-market risk assessment
When post-risk assessment is discussed, people often ask about pre-market risk assessment.
There is no specific template for pre-market risk assessment. However, for electrical goods, there is CENELEC Guide 32 (CENELEC is the European Committee for Electrotechnical Standardisation).
The purpose of these assessments is to manage the risk before placing the product on the market and Standards are a good place to start.
Further information
The Regulators' Code, is "a framework for how regulators should engage with those they regulate".
The Office for Product Safety and Standards (OPSS) has produced a list of Designated Standards that businesses can use to show that they comply with legislative requirements.
OPSS has produced guidance on conformity assessment and accreditation, which includes information on the effects of leaving the European Union on the law in Great Britain.
OPSS has also produced an Incident Management Plan, which contains information on OPSS's framework for recognising and responding to product safety-related incidents.
OPSS's Primary Authority Overview explains the main features of the Primary Authority system, which allows businesses to enter into a relationship with a particular local authority (or authorities) to receive assured and tailored advice.
Product Safety Risk Assessment Methodology (PRISM). This link provices information from OPSS on the risk assessment methodology for use by those authorities in Great Britain that have responsibility for consumer product safety.
Back to top